TRAINING
Along with products and services, DG Technologies offers world-class training classes to provide a thorough understanding of the various automotive networks. Classes are taught by instructors who are experts in the vehicle network industry and include several hands-on training opportunities. Seminars are taught at the DG Technologies Headquarters in Farmington Hills, MI or class materials can be customized for a company and taught on location at their site.
Note: Materials and fees may fluctuate depending on training needs, materials, and class location.
Available Training Courses
Heavy Duty Protocol Training
Course Outline
Date: June 20th-June 21st, 2024
- DAY ONE
- Introductions
- Day 1 Terminology Preview
- On-Vehicle Networking History
- Industry Connectors Reference
- Computer Science Fundamentals Required for Vehicle Protocols
- J1708/J1587 and PLC4TRUCKS
- J1708/J1587 Hands-on Lab Exercises
- Introduction to CAN (ISO11898)
- CAN Physical and Data Link Layers
- CAN Frame Structure, Bus Arbitration, and CAN Error Handling
- CAN Physical Network Troubleshooting
- The Next Generation of CAN, CAN FD (CAN with Flexible Data Rate)
- TMC RP1210 and J2534
- DG’s Adapter Validation Tool (AVT) and DG Diagnostics (DGD)
- DAY TWO
- Day 1 Terminology Review and Day 2 Terminology Preview
- J1939 In a Nutshell
- J1939 Protocol Layering
- J1939 Physical Layers
- /11 – Shielded Twisted Pair, /15 – J1939 Lite, /14 – J1939@500k
- J1939 Diagnostic Connectors
- Type I and Type II
- J1939 Data Link Layer
- J1939 Network Addressing
- J1939 Transport Layer
- J1939 Message Layer
- J1939 Diagnostic Layer
- J1939 Hands-on Lab Exercises
Course Cost: CALL FOR QUOTE
*On-site courses are available by request as well as a short 1 day version.
Introduction to Car Hacking with CANbus
The objective of this course is to introduce modern automotive in-vehicle communication networks, the CAN communications protocol and the OBD-II interface threat models, hacking into the OBD-II diagnostics interface, ECU cracking, and vehicle network cyber penetration testing.
This course will cover existing in-vehicle communication protocols and associated vulnerabilities. Student would be able to learning principles of ECU hacking techniques and understand penetration testing for automotive CAN communications systems.
This course will cover the limitations of existing digital forensics. A hands-on lab will be used to provide learning experience in various aspects of in-vehicle communication ranging from data acquisition to diagnostics, anomaly detection, car ECU hacking.
Vehicle cyber-security vulnerabilities could impact a vehicle’s safe operation. Therefore, engineers should ensure that systems are designed free of unreasonable risks to motor vehicle safety, including those that may result due to existence of potential cyber-security vulnerabilities.
The automotive industry is making vehicle cyber-security an organizational priority. Prioritizing vehicle cyber-security also means leaning about vehicle hacking techniques in order to ensure that systems will be reasonably safe under expected real- world conditions, including those that may arise due to potential vehicle cyber-security vulnerabilities from hacking the CAN communications or OBD-II interface.
The automotive cyber-security environment is dynamic and is expected to change continually and, at times, rapidly. Developing a basic understanding of car hacking can provide a good foundation for developing approaches to vehicle cyber-security. This course material will can be maintained, refreshed and updated periodically over time to serve the needs of the automotive industry.
Prerequisites
Participants should have a bachelor’s degree in engineering, computer science or equivalent. A background or some experience with automotive electronics and vehicle systems is recommended.
Learning Objectives
By attending this seminar, you will be able to:
- Recognize basics of cyber-security
- Determine SAE and other industry standards related to automotive cyber security
- Identify basics of threat models for automotive systems
- Acquire and analyze in-vehicle communication data
- Hack ECUs
- Use tools for vehicle anomaly detection
Course Outline:
(SAE J2534, J2248, J1939, J3061, J3005, J3138)
(ISO 15765, ISO 14229, ISO 27145)
Date: TBA
- DAY ONE
- Introduction to applied cybersecurity best practices
- Introduction to threat models for automotive systems
- In-vehicle communication networks and protocols
- CAN-bus vehicle communication
- Relevant SAE and ISO technical standards
- DAY TWO
- OBD-II and CAN-bus diagnostics
- Reverse engineering CAN-bus
- Tools of the hacking trade
- Penetration testing demo
- Hands-on ECU hacking
- Sensor disruption
- DOS attack
- Message spoofing
Course Cost: CALL FOR QUOTE
LIN Overview
LIN is a leading edge and relatively low cost network often used to augment a CAN network for body and chassis electronics. It is replacing older protocols such as J1850 and K line (ISO 9141), where the bandwidth and flexibility of CAN is not required.
You will learn the LIN protocol, configuration language and the API. The differences between the various versions of LIN and the SAE standard are also discussed. A demonstration illustrating how LIN frames are constructed and their architecture is given.
Learning Objectives
To give students an in-depth knowledge of LIN and its different implementations.
Prerequisites
Engineers and technical personnel. Knowledge of in-vehicle networking is helpful, but not necessary.
Course Outline
DAY ONE
• Introduction: General LIN Overview
• Where LIN is used; hardware requirements
• LIN protocol – 1.2, 1.3, 2.0 and SAE J2602
• LDF – LIN Descriptor Files – Demystifying the LDF
• Schedule Tables: What is a Schedule Table?
Course Cost: CALL FOR QUOTE
When: To Be Determined
Time: To Be Determined
Where: DG Technologies
33604 West 8 Mile Road
Farmington Hills, MI 48335
This course is the second course in a series of Automotive Ethernet fundamentals courses and builds on current “Basics of Automotive Ethernet and Physical Compliance Workshop”.
This session will focus on the upper layers (L2-7) and devices used in an Ethernet network. Special attention will be given to the Autosar and Open Alliance TC8 test specification and ways of simplifying the testing.
The following topics will be covered:
- Ethernet Layer 2 and above
- Automotive Ethernet Protocols
- Conformance testing
- Ethernet Networking
- Bridging/Switching
- Performance testing
- OPEN Alliance TC8 Test Specifications
- Autosar Conformance Test Suite
- Autosar Testability Protocol and Service Primitives Specification
- Testing Methodologies
- Test Scope Layer 2 of Automotive Ethernet
- Test Scope TCP/IP Protocol Family
- Test Scope Automotive Protocols
Who should attend: Engineers and Technicians looking to learn more about the testing for Automotive Ethernet/BroadR-Reach.
What attendees learn: Practical understanding of the upper layers of Ethernet as well as testing methodologies.
CALL FOR QUOTE
Email: sales@dgtech.com
Diagnostics CAN-Basic OBD
Beginning in 2007, CARB and EPA require ISO 15765 DiagnosticsOnCAN for light vehicles. This course will prepare you to design, develop, test and work with this protocol.
Learning Objectives
This course examines ISO 15765 (DiagnosticsOnCAN) with a brief introduction to its predecessor, KWP2000 plus OBDII, J1979, J2012, J2190 and J2284. This information will also be useful for J1939 users who choose to use ISO 15765 for the upcoming legislated heavy duty vehicle emissions requirements.
SAE J1979 SID’s along with their associated PID, MID, TID and INFOTYPES will be discussed and utilized.
You will learn how parts of these protocols are used to create DiagnosticsOnCAN. You will gain: A good overall knowledge of DiagnosticsOnCAN (OBD).
Prerequisites
Engineers and technical personnel. An understanding of CAN is helpful but not necessary.
Course Outline
- DAY ONE
- In-vehicle network overview
- CAN protocol – physical and data link layers
- Overview of J2411, J2284, OBDII, UDS
- DiagnosticsOnCAN (ISO 15765), J1979
- On-site courses are available by request
Course Cost: CALL FOR QUOTE
CAN and Higher Layer Protocols
CAN (Controller Area Network) is today’s worldwide standard for in-vehicle and factory floor automation networks. If you would like a fundamental background on CAN and some of the most popular messaging protocols layered on top of CAN, this will be the class to attend.
There are two hands-on laboratory sessions designed to solidify the classroom fundamentals. These examples will show how to request and decode data from the J1939 and ISO15765/J1979 networks.
Learning Objectives
The student will first gain a good familiarity of CAN network theory, application, and troubleshooting. The course then dives into the various message layers that have been written for CAN such as ISO15765 and J1979 (DiagnosticsOnCAN) and the heavy-duty industry standard called J1939. Amongst the training modules are introductions to the programming standards supporting the CAN protocols, SAE J2534 and TMC RP1210.
Prerequisites
Previous knowledge of network protocols is a plus, but not necessary.
Course Outline
(CAN, CAN FD, ISO15765, J1939, J1979, RP1210, J2534)
- DAY ONE
- On-Vehicle Networking History
- Computer Science Fundamentals Required for Vehicle Protocols
- Introduction to CAN (ISO11898)
- Physical and Data Link Layers
- CAN Message Structure and Bus Arbitration
- Network Troubleshooting
- Next Generation CAN, CAN FD (CAN with Flexible Data Rate)
- J1939 and Hands-on Lab Exercises
- Introduction to TMC RP1210
- J1979 Using CAN and Hands-on Lab Exercises
- Introduction to SAE J2534
Course Cost: CALL FOR QUOTE
To Register for Classes, Call 248.888.2000 or email sales@dgtech.com
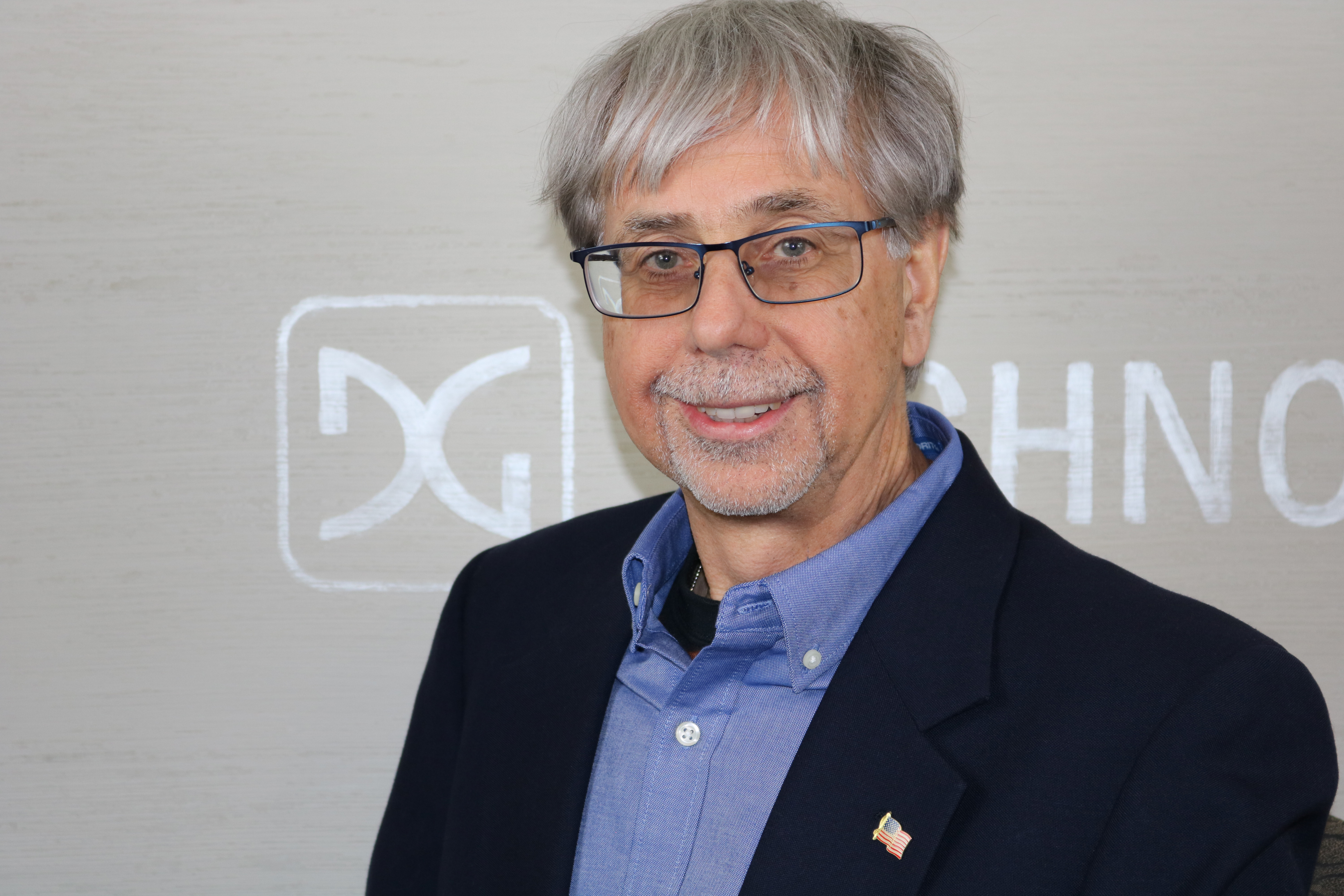
Instructor: Mark Zachos
The Founder of The Dearborn Group Inc and President of DG Technologies. Mr. Zachos has over 30 years of engineering experience in automotive electronics, cyber security, vehicle diagnostics and communications. He has authored many technical papers on On-Board Diagnostics (OBD) and in-vehicle networking; he holds more than 10 patents on vehicle communications technology. Mark is the Head of USA Technical Advisory Group (TAG) to the International Standards Organization (ISO) Road Vehicle Electronics Standards Sub-committee; he is a member of TMC, SAE and IEEE; he has been directly involved with development of over 25 light and heavy-duty vehicle technical standards. Mark is the chairman of several technical standards teams including: the American Trucking Assoc. TMC Fleet Maintenance Cyber Security Task Force, SAE J1939 Network Security Task Force, SAE J3005 (OBD “dongle” security), SAE Data Link Connector Security Committee (i.e. SAE J3138 “hardening the OBD port”) and co-chair of ISO/TC22/SC31/WG2/PT-Security. He also is a member of the Oakland County (MI) Connected Vehicle Task Force focusing on secure connected vehicle deployment; teaches embedded programming, CANbus and vehicle cyber security at The University of Michigan-Dearborn; instructs hackers at the US Army TARDEC CyberTruck Challenge; and established CyberTech – the TMC service technician troubleshooting skills challenge for identifying and repairing vehicle cyber hacks.